Understanding Sandblasting Compressor Size Requirements
By
on Mar 24th 2021Click here to use our Interactive Compressed Air Requirement Tool
When it comes to sandblasting, there are many different factors that come into play before you can even get started. Some of the biggest questions involve the blast pot itself: What are the different capacities of the various models? Which size is right for a particular application?
An often overlooked piece of the buying process, however, is the compressor. The compressor is especially important because it powers the entire operation. Here, size matters. In most cases, a standard shop compressor will not be large enough to pressurize the blast pot.
In reality, a blast machine is a large pneumatic tool driven by compressed air.
The Blast Pot
To operate the machine, the blast pot requires a minimum 50 PSI just to seal the pop-up valve. A sealed pop-up valve pressurizes the pot. The blast pot’s optimum operating pressure is 90 PSI—this ensures the most efficient and effective blasting. Once pressurized, the compressor requires enough air flow to keep the pot at its minimum 50 PSI while still having enough CFMs to allow pressure out at the nozzle. If your compressor can’t keep up with the amount of air you are releasing at the nozzle, the pop-up valve will unseal and all pressure will be lost. No pressure means no blasting.
One way to think of this scenario is to imagine that you got a nail in your car tire pressurized at 40 PSI. Your tire (Blast Pot) was under pressure until you got the nail in there. If you pull the nail out of the tire, you have a hole (Nozzle Orifice) in which the air is escaping and PSI is decreasing. A certain amount of air pumped into the tire will keep it inflated (pressurized) as long as the air is not escaping out of the hole faster than it is being pumped in. If the volume (CFM) is high enough, you can actually maintain 40 PSI despite the hole. The larger the hole, the more air is required to keep the tire inflated and maintain 40 PSI.
Keep this in mind for your blast operation .
If you increase your nozzle orifice size or the PSI at which you wish to blast, you will also be increasing the volume of air required to keep your blast pot pressurized.
Our chart below illustrates the CFM requirements for different nozzle sizes at different pressures. This will help you in determining compressor size.
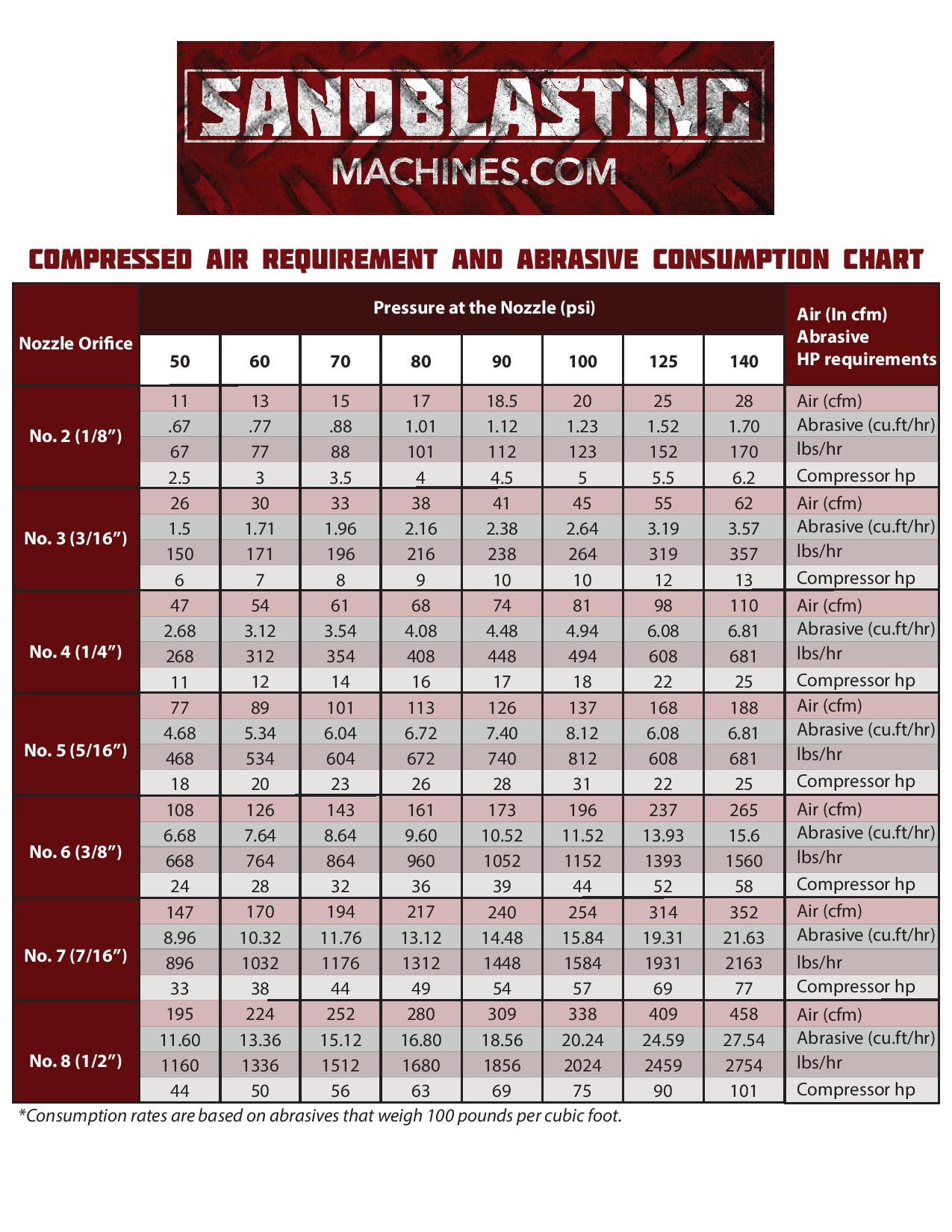
Click here to view or print the full-size Compressed Air Requirement and Abrasive Consumption Chart
The Respirator
Another factor you need to consider is your breathing air respirator. High-pressure (HP) systems require a breathing air compressor and an additional 20-25 CFMs to supply enough air to the operator. Low-pressure (LP) systems utilize ambient air pumps and therefore don’t affect compressor size.
Practical Application
Here is an example of a typical Clemco blast pot set up:
An operator blasting with a Clemco TMP- 5 Nozzle, 5/16” Orifice at the minimum 50 PSI would require a compressor putting out 77 CFMs. Again, keep in mind that an additional 20-25 CFMs will be required for an HP respirator system, such as the Apollo 600 HP Breathing Air Respirator. This puts you at a total of 97-102 CFMs. If you are blasting with a larger nozzle, such as the Clemco TMP-7 Nozzle, 7/16” Orifice, your CFM requirements will increase.
At the minimum 50 PSI, a 7/16” orifice nozzle will require 147 CFMs. As you increase the pressure going into the pot, the amount of CFMs needed at the nozzle will increase as well. The same TMP-7 Nozzle blasting at the optimal 90 PSI will require 240 CFMs to keep up with the amount of air being put out at the nozzle.
If you’re uncertain whether your compressor is large enough for your sandblasting needs, remember to keep in mind both the PSI at which you’ll be blasting as well as the nozzle size.
Still have questions? Send us a chat, email, or give us a call—we’re more than happy to help you with your sandblasting needs.